Toys
It was pointed out to me in the comments for my article on parallel grooves that one of the most ingenious uses of this technology is in children’s toys, the classic example being the See & Say – a pull-string toy that plays a variety of randomized prerecorded sounds. There have been many designs over the years, but they all look something like this:
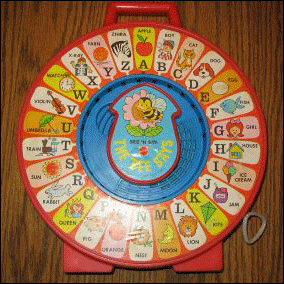
Pulling the string sends the arrow spinning around. The area on the perimeter where the arrow lands determines which sound will be played. This playback is achieved using a plastic disc with numerous parallel grooves. In the photo below you can see the lead-in groove to each of the parallel samples along the edge of the disc – each of these lead in grooves corresponds to one of the selections on the perimeter of the See & Say.
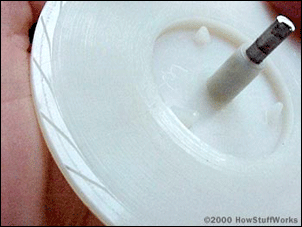
The grooves are played by a stylus that is attached to a plastic cone. The stylus transmits the vibrations to the cone, which acts as the ‘speaker.’ There are no electronics whatsoever. You can see an example of the stylus / cone machanism below.
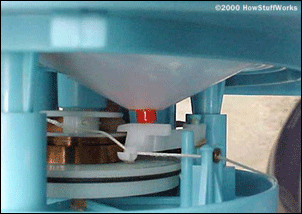
These photos came from How Stuff Works, a site that has a more elaborate explanation of the inner workings of the See & Say on this page. The same principle was used in some pull-string talking dolls with multiple ‘sayings.’
Earlier talking dolls – manufactured to use Thomas Edison’s then-new sound reproduction technology – employed simpler mechanisms. Edison’s first attempt to capitalize on this idea failed, though he eventually managed to turn a profit after letting someone else do the work for him. A quote from this site:
“Despite several years of experimentation and development, the Edison Talking Doll was a dismal failure that was only marketed for a few short weeks in early 1890. Edison had envisioned the idea of a talking doll as early as 1877, but it was another inventor, William W. Jacques, who first developed a prototype based on Edison’s original tinfoil phonograph. Jacques and his partner Lowell Briggs founded the Edison Phonograph Toy Manufacturing Company in 1887 with Edison agreeing to lend his name to the planned product in return for royalties and stock ownership. Before production began, however, Edison took over the company, demoting the founder and leading to years of ill-will and lawsuits.”
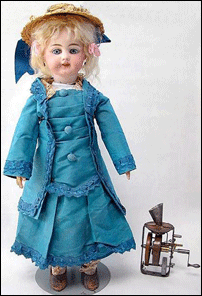
Self-amplified Records
Another anomaly I accidentally found reference to while researching my previous articles on vinyl stuff was this promotional item for Skippy Peanut Butter – a record with the player built in. The sound was reproduced by spinning the record with a pencil and resting a pin, attached to the cardboard horn, in the groove of the record.
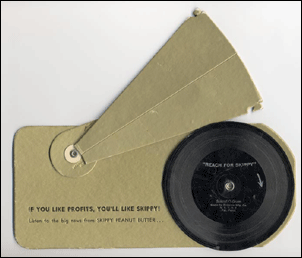
The Skippy item is described on The Internet Museum of Flexi / Cardboard / Oddity Records:
“It’s a crude sound and I wonder how this was thought to be the proper medium for the Skippy Peanut Butter company to send their message. This is the only product I’ve seen by Sound-O-Gram, the company that manufactured this. It is a simple and effective mechanism for sound reproduction. About 78 rpm, 195?.”
You can view the instructions here, and watch a short clip of the device in action in Realvideo format.
Vinyl Home Recording
An interesting sidenote in the history of grooved playback are ‘blank’ records. Many different companies marketed records that enabled the purchaser to crudely record sound using their home phonograph. These records were primarily made of metal – a good gallery of several examples can be found here.
The ‘Repeat-a-Voice Metal Recording Discs‘ printed the following instructions on the sleeve:
“Put a ‘Repeat-a-voice’ metal recording disc on your phonograph. Use an extra loud needle and a small megaphone. Then talk or sing into the horn [speaker]. That’s all! Play the record and you’ll hear your voice.”
I’ve included an image of the sleeve below. These discs operated on a simple reversal of the principle normally used to play records. Instead of the needle transmitting vibration to the speaker, the speaker was used to transmit vibration to a hard cutting stylus. You can view an image of the webhost of the The Internet Museum of Flexi / Cardboard / Oddity Records recording such a record here, and listen to the resultant recording here (Realaudio format).
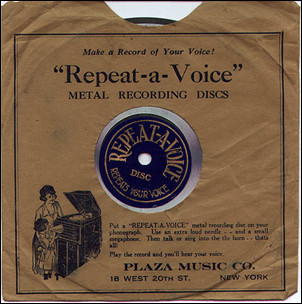
This practice of using a speaker as a microphone is still used in some capacity today. Many recording engineers maintain that this is a sure-fire way to capture low frequencies when recording bassy instruments such as the kick drum of a drumkit. This has become so entrenched in recording engineer lore that Yamaha has begun marketing a ‘SubKick Low-Frequency Capture Device’ (MSRP $299.99), as seen below. Detailed information can be found here, and all sorts of fun threads particularly dealing with the Yamaha product and the theory behind it can be found via the Tape Op message board (links: 1, 2, 3, 4, 5, 6, 7).
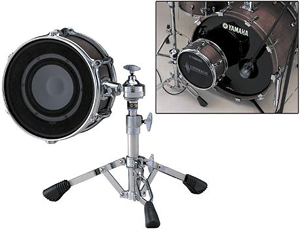
As technology improved, slightly more advanced methods for recording records were devised. One such example is the Recordio, which used a microphone element to directly impart the sound to the cutting stylus. The coin-operated recordios appealed to the novelty of recording messages in one’s own voice by offering the recordio-gram. Home-use recordio machines were also eventually produced.
Before rushing off to ebay to get your hands on a vintage recordio machine to screw around with, be aware that the problem of finding quality blank media to record on is an issue among the diehard community of people still tinkering with them. Some discussion grabbed from the newsgroups:
“…a very
important thing is age. Back in the days when disc recording was
commonly in use, you always bought the freshest softest discs that you
could find. If you could nick the lacquer with your fingernail, you
had a good disc. The lacquer hardens with age, and no longer cuts
quietly, but with a rushing, scratchy sound. I have several NOS
recordio discs, but they cut a pretty lousy record.”
…
“I use the clear sheets used for spiral notebook covers (the kind that you put > 3 holes in and screw a spiral in). I cut it into a circle and then cut a hole in the center. Depending on how deep the machine makes grooves, you may be able to record on one side or both.”
If this sort of thing fascinates you, there’s a decent history of such devices here, with all sorts of nerdy tangents to follow up on.
CD-RPM
After noting my unhealthy obsession with vinyl trickery, George V. told me about a band called Nautical Almanac, who have been doing some great stuff using a dictaphone (A device similar to the Recordio mentioned above) and CD-R’s. I wrote to the band asking about their process and got a detailed reply from member ‘Twig’ Harper:
“We [currently] have our own lathe. For the longest time we used an old dictaphone
transcrition machine which cuts tighter grooves – the fidelity is
horrible but it was all we had. We could fit about 8 mintues on the
information side of a cd, and we made a ton of these from 1997-2001. Once we got a CDR burner, we put half cd info and half grooves on one
format, which saved our ass cutting-wise because you have to cut in
real time which is a lot of hours sitting down. The machine [was] slowly dying, [and] it finally did after we finished our 2003
summer tour-only release (Did about 200 of those). We had our friend
work on our Presto 6N lathe and he got it up to par. We have an RCA head on
it now which sounds a little better than the original presto head. We still need to get a proper amp to drive it but we have a rigged set up. We
will probably make a few hundered cdr/recs for the Nautical Almanac
tour we’re doing this June/July….
The major problem with the old
dictaphone set-up was figuring out the right material to cut on. Nate
Young worked on figuring this out – [he tried] plastic soap detergent
bottles, ‘solo’ brand plastic plates – anything soft plastic was used.
One day after sitting around, the idea of cutting onto cds magically
appeared in our heads – duh… – seems so simple in retrospect but for a
year or two we didnt think of it. The next step was to figure out a way
to hold the cd in place, so I had to glue a cd tray to the spinning
platter and then tape the cd down to get a centered cut.
I’m really happy the thing died… it was a pain in the ass.”
Twig sent along photos of the dictaphone and a CDR with grooves cut into it, which I’ve included below:
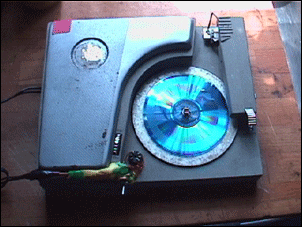
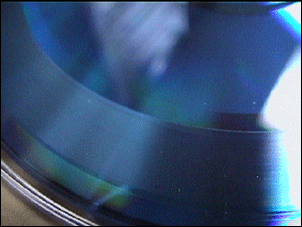
Mr. Harper also discussed some of the new challenges he’s encountered owning his new presto lathe, so if you’re a lathe expert, feel free to get in touch with him. You can visit Nautical Almanac’s website here.
“The only problem with the presto is that i can only fit about 1 1/2 minutes
until the feed on the head stops. I hear there is a way of modifying
the 6n so you can cut all the way to the center if you want. Ill have
to call up someone in the secret society of lathe trolls to get this
information and trade some semi precious materials. The fideleity
is pretty insane with the presto, but ive only had it fixed for a little
bit so I’ll see what other problems come up. Right now, everything is sold out, but we’re getting ready for tour and will be making runs of some lathe cut cdrs and recs.”